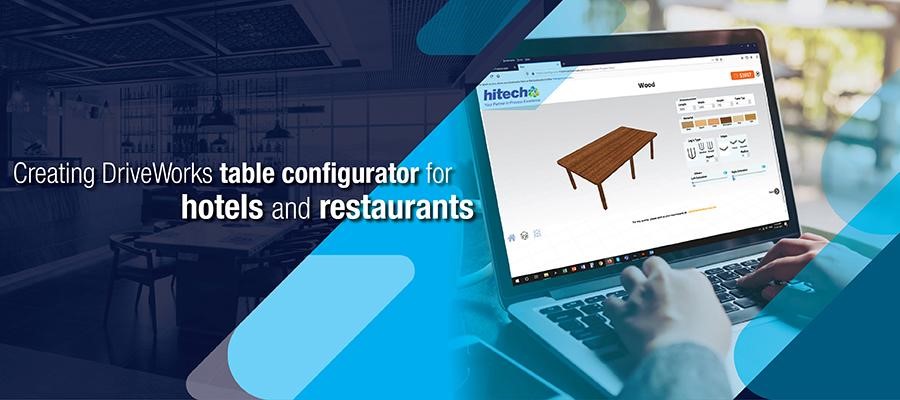
Hospitality industry furniture goes out of trend faster than their operational lives. To meet the industry trends, manufacturers use automated solutions like table configurators using DriveWorks to get dressed for success.
Hospitality industry faces fast-changing design trends propelling competitiveness amongst manufacturers and designers as well as reduced delivery lead times. Restaurants and hotel owners want to set the place running, they are in a hurry to get the final furniture delivered on time. As a result, designers and manufacturers are pressed against tight deadlines for design and manufacturing.
To overcome these challenges, hotels and restaurant furniture manufacturers see the deployment of an automation tool, a configurator. It accelerates the design cycle and delivers up to 99.99% error-free drawings and 100% custom pricing accuracy.
A 3D configurator is the best solution to accelerate furniture design cycles
Deploying a 3D product configurator using DriveWorks expedites the design cycle by 70% and brings down the design cycle time from 4-5 days to a few minutes.
- The powerful rules engine does the heavy lifting for design specification and creating 2D manufacturing drawings and models.
- Product configurator captures design intelligence from master CAD models and reuses it to assign user-specific design inputs.
- Multiple-rules, forms, design layers, and macro automation at work help achieve faster design cycles.
While there is a range of furniture for the hospitality industry, let us consider the example of a table – the most commonly used piece of furniture.
Step to customize a table with DriveWorks table configurator
Here’s a series of steps that helps users customize tables as per their need, and enable design engineers and managers to achieve faster design cycles.
1. Select your niche within hospitality
Tables [or any other furniture piece for those matters] vary largely across various industries, and sometimes even within the industry.
For example, a table made for food preparation at a caterer’s shop is narrower and has several decks to store tools. While a coffee table at a café is larger, has good looks, and usually has a short height.
So the users need specific tables tailored to their intended application and environment of use.
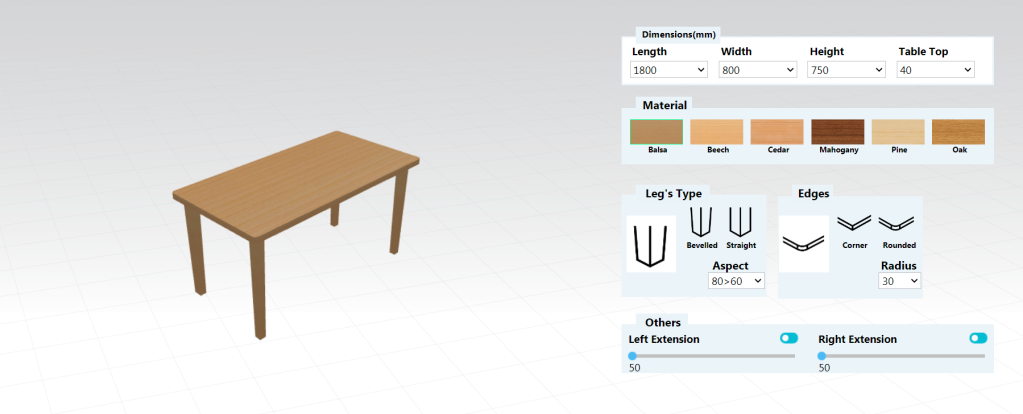
By deploying a table configurator, you essentially allow your customer to land on a specific page and design catalogue suitable for industry-specific needs. Here the user can choose the table design specs as per his needs and the suggestions displayed will be in accordance.
Focused options eliminate design cycle errors rising from inconsistent geometry, under the capability of manufacturing tools, an anomaly in designs, etc.
So when the user enters the configurator portal for conference tables, the basic model is like the skeleton of a standard oval or huge rectangular table. And from here the user can enter a bespoke design specifications interface.
2. Populate your design specifications to the intuitive interface of the configurator
Based on the theme of your restaurant and hotel interiors, you will want to have a table’s form and finish. This is done easily with 3D product configurators by taking specific inputs from the user with step-by-step assistance.
A product configurator asks the user to fill up a series of forms to specify their design inputs. In the case of tables, it starts with the type of primary material whether it is wood, metal, or hybrid. Next, is the surface finish needed and color.
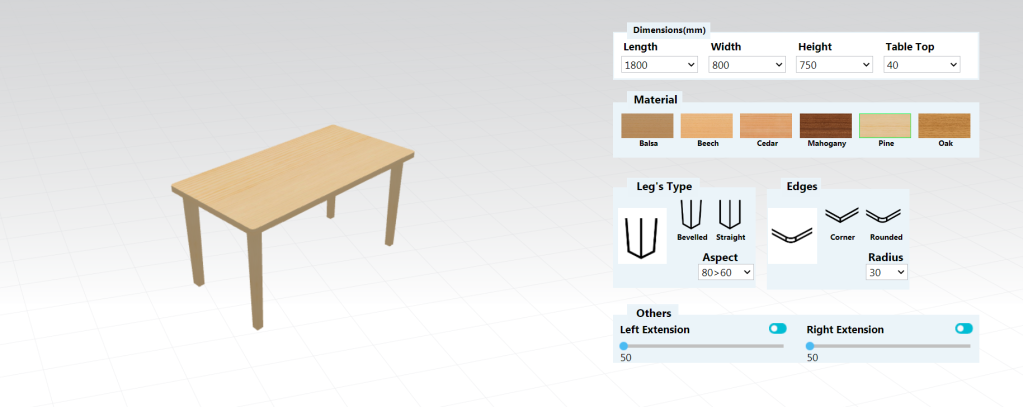
From there the configuration goes to the top covering, veneer selection, grains, the color of the wood, type of wood, to all the way to detailing of corners: rounded or sharp; legs: beveled legs or not, etc.
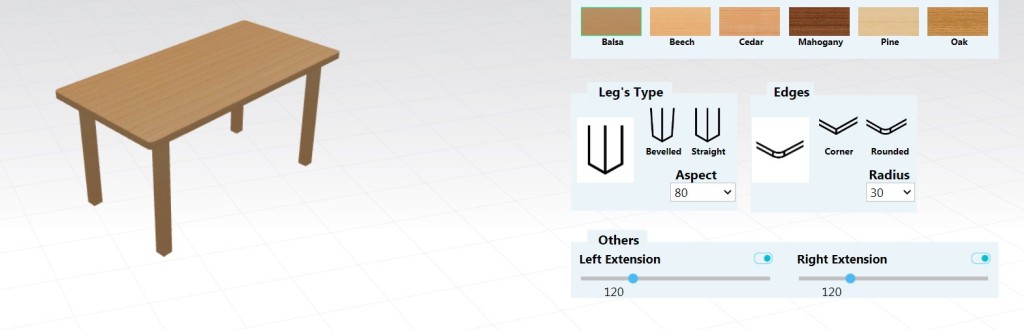
As the forms get displayed in a sequential manner on screen, the user gets to select a value ranging between upper and lower ranges of pre-set dimensions. At the same time, the product configurator will showcase a real-time 3D model of the user-specific inputs.
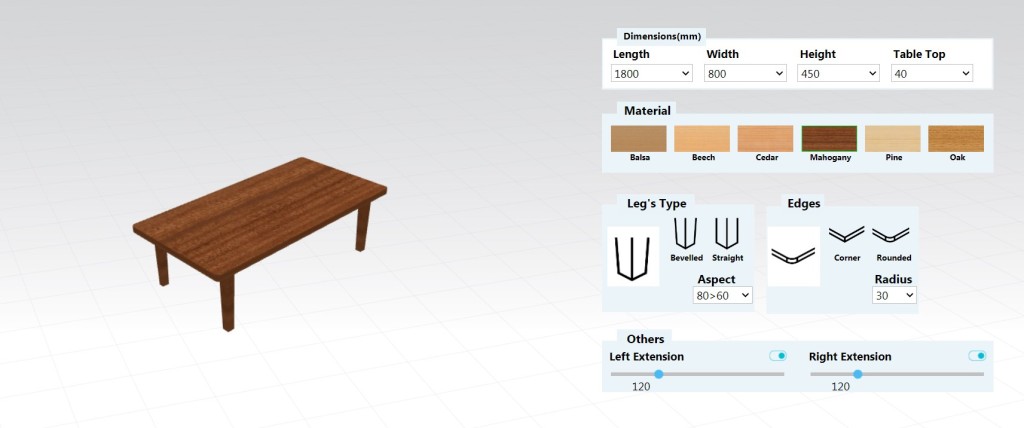
3. Automatically generate and get your documents over emails
Once you have given your choice for design specifications, DriveWorks automatically creates custom sales documents and manufacturing drawings for your orders. Simultaneously, the price is shown for every specification on the top right corner.
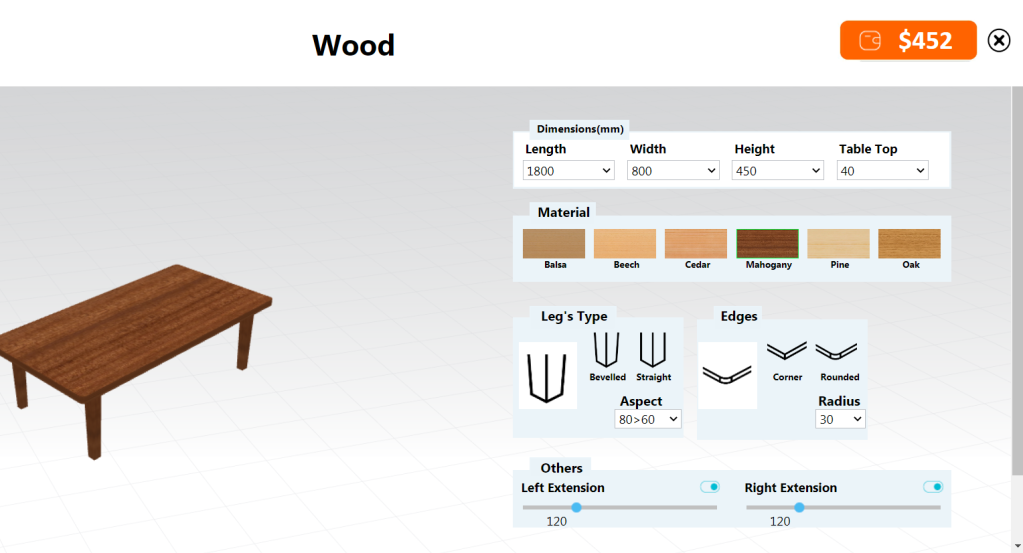
When you are done populating the specifications, you can view the Bill of Materials [BoM] and respective sales quotes for the order by clicking on the next page. The automated solutions for BoMs will show you a complete summary of the ordered product.
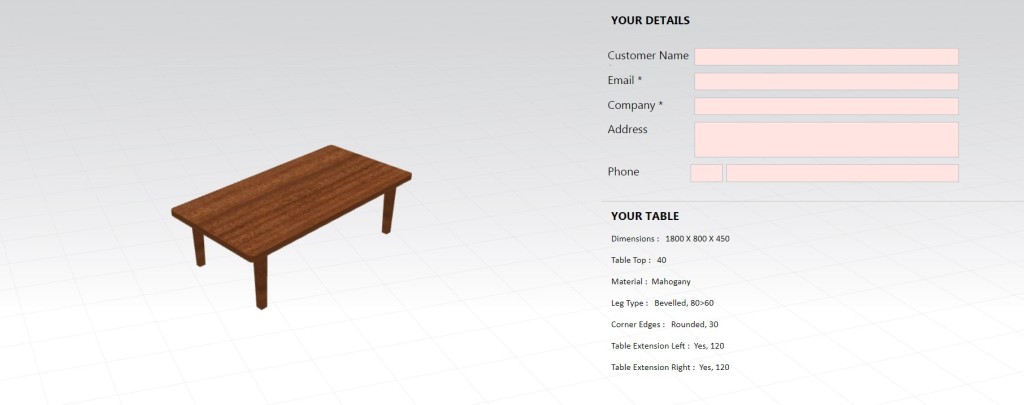
So when you/your sales team/your customer – the hotel or restaurant owner – confirms/ the order, DriveWorks table configurator generates the assembly and part drawings for the said dimensions of the table. The automated tools for manufacturing drawings share the relevant documents with manufacturing engineers on the shop floor.
4. Place your order to generate custom manufacturing drawings
Once the orders are confirmed, engineers, at the back end, receive manufacturing drawings from the configurator with details for tables’ design features. As these drawings are generated automatically through preset rules based on engineering knowledge, they are 100% error-free. It saves time in QC and can be sent directly to the manufacturing shop floor.
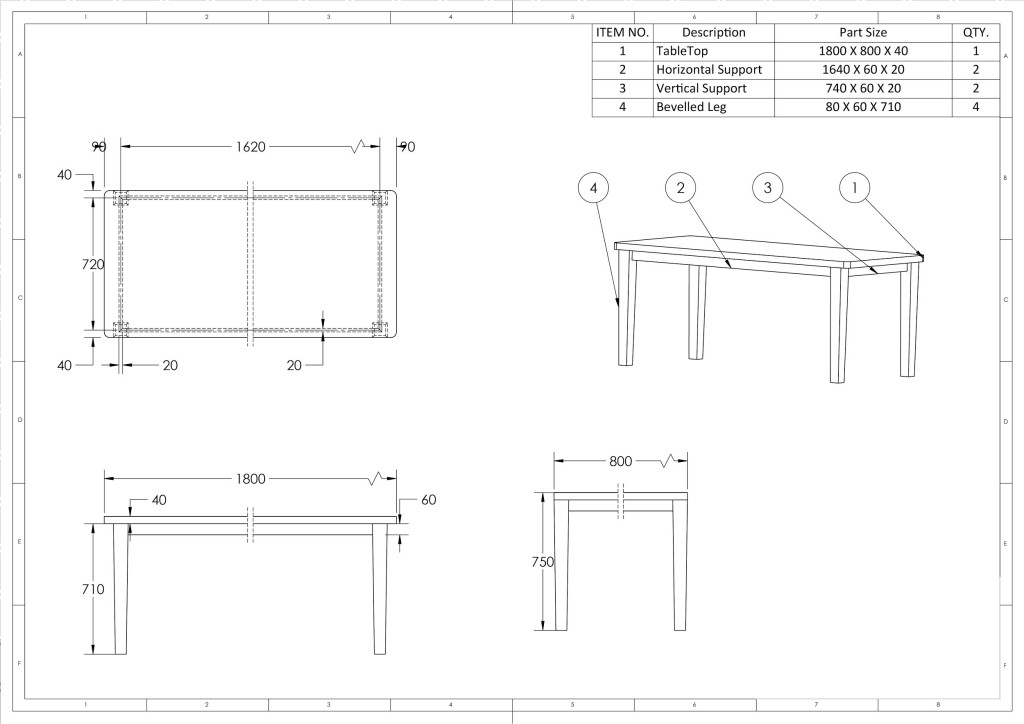
All the drawings created are labeled with part numbers as per the client firm’s nomenclature as well as the description. Automation will not only reduce time in searching a particular drawing but also eliminate long engineering man-hours every time a new order is received.
Additionally, if you are partnering up with a DriveWorks authorized service provider, they help you update the master models, logical rules, user-forms regularly to meet the latest design trends. They also help you with DriveWorks plugin development with which you get to enhance your product configurator tasks.
Deploying a DriveWorks table configurator with experts
Designing tables (and other furniture) using a configurator saves a huge amount of time for the hospitality industry. These are really helpful when you are refurbishing your interiors and want new furniture, while your space is not operational. You’d naturally want the furniture done faster. And table configurators help you achieve that exactly.
Working with a DriveWorks expert can easily enable you to leverage advanced features of DriveWorks Pro module and develop custom APIs that support 3rd party integration. An expert DriveWorks implementation service provider can help you connect your business database such as CRM, ERP, SCM, etc. to DriveWorks and achieve faster turnaround times.